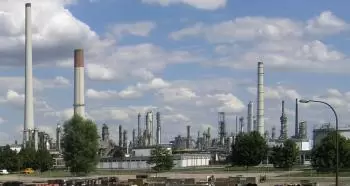
Una refinería de petróleo es una planta industrial que transforma el petróleo crudo en productos útiles mediante procesos como la destilación y purificación. A través de técnicas como la destilación a presión normal y bajo vacío, el petróleo se separa en fracciones con un intervalo de ebullición definido.
Estas fracciones se refinan aún más usando métodos como la extracción o limpieza química. Para mejorar la calidad de los productos, como el índice de octano, se emplean procesos de conversión como la isomerización o el reformado catalítico. Además, se añaden aditivos a los productos para mejorar o modificar ciertas propiedades.
Los productos obtenidos incluyen combustibles de alto valor, como gasolina, diésel, queroseno y gasóleo. También se generan materias primas para la industria química, como gas licuado de petróleo, nafta y destilados medios.
Las refinerías de petróleo son grandes complejos industriales, compuestos por tanques, columnas de rectificación, sistemas de tuberías y bengalas. Estos negocios son muy intensivos en energía, ya que hasta el 50% de los costos de producción provienen de la energía, que se suministra principalmente desde los propios productos energéticos.
El petróleo: la materia prima de una refinería
La materia prima de una refinería es el petróleo crudo, una mezcla compleja de hidrocarburos. Los principales tipos de hidrocarburos presentes son los alcanos (parafinas), los cicloalcanos (naftenos) y los aromáticos. Cada tipo de petróleo tiene una composición química específica que depende de su origen, lo que también influye en sus propiedades físicas, como el color y la viscosidad.
El petróleo crudo también contiene compuestos con nitrógeno, oxígeno y azufre, como aminas, porfirinas, mercaptanos, tioéteres, alcoholes y quinonas. Además, puede incluir trazas de metales como hierro, cobre, vanadio y níquel. La proporción de hidrocarburos puros varía entre el 97% y el 50% en los aceites más pesados. El contenido de carbono está entre el 83% y el 87%, y el de hidrógeno entre el 10% y el 14%. Otros elementos, como los compuestos metálicos, son generalmente inferiores a 1000 ppm.
El petróleo crudo varía según la región. Ejemplos conocidos incluyen el West Texas Intermediate (WTI), un crudo ligero de bajo contenido de azufre; el Brent Blend, proveniente del Mar del Norte; y el crudo pesado de Tapis de Malasia y Minas de Indonesia, entre otros.
¿Qué productos se obtienen en una refinería?
Los productos terminados de una refinería pueden ser gaseosos, líquidos o sólidos.
En una refinería moderna, aproximadamente el 3% de los productos son gases licuados como propano y butano, el 9% son derivados como nafta, y el 24% es gasolina. Otros productos incluyen queroseno (4%), diésel (21%), combustible pesado (11%) y productos sólidos como betún (3.5%) y lubricantes (1.5%).
El rendimiento de los productos depende de la naturaleza del crudo procesado y de la configuración de la refinería. Los crudos ligeros, por ejemplo, producen más productos livianos como GLP, gasolina y queroseno, mientras que los crudos pesados generan más productos pesados como el fueloil. Además, las refinerías modernas pueden utilizar procesos como el craqueo para convertir estos productos pesados en otros más ligeros.
¿Cómo funciona una refinería de petróleo?
El petróleo crudo extraído de los depósitos se somete a un tratamiento preliminar para eliminar impurezas como sedimentos y agua. Luego se transporta a la refinería, donde se somete a un proceso de destilación para separar sus componentes en fracciones con diferentes puntos de ebullición. Estos componentes se procesan para producir productos terminados.
Uno de los subproductos del proceso es el gas de refinería, que se utiliza como fuente de energía en los hornos o en procesos químicos.
Purificación y desalinización del petróleo
Antes de la destilación, el petróleo crudo se desala para evitar la corrosión en el equipo. Este proceso implica agregar agua al crudo para formar una emulsión que se separa en un desalador electrostático. El aceite crudo desalado se bombea luego a la unidad de destilación.
Procesamiento primario: Destilación del petróleo crudo
El crudo desalado se calienta en dos etapas: primero en intercambiadores de calor, y luego en hornos hasta aproximadamente 400°C. Después, se somete a destilación en una columna de hasta 50 metros de altura. En este proceso, el crudo se separa en diferentes componentes según sus puntos de ebullición, como gasolina, queroseno, diésel y residuos.
Los residuos de esta primera destilación se someten a una destilación al vacío para obtener productos como gasóleo al vacío y otros subproductos.
Procesos de conversión y mezcla
Para mejorar la calidad de los productos y eliminar contaminantes como azufre y nitrógeno, se utilizan procesos adicionales como el hidrotratamiento, el reformado catalítico, la isomerización y la alquilación.
- Hidrotratamiento: El petróleo crudo es tratado con hidrógeno para eliminar compuestos de azufre y nitrógeno.
- Reformado catalítico: Este proceso mejora el octanaje de la nafta y produce hidrocarburos aromáticos, además de generar hidrógeno.
- Isomerización: Los alcanos se convierten en isoalcanos para mejorar el octanaje.
- Alquilación: Se combinan isoalcanos y alquenos para formar hidrocarburos de mayor peso molecular y alto octanaje.
Craqueo
El craqueo térmico, catalítico e hidrocraqueo se utilizan para romper cadenas de hidrocarburos pesados y producir productos más ligeros, como gasolina y diésel. En el craqueo térmico, se aplica calor sin catalizadores, mientras que en el catalítico y el hidrocraqueo se emplean catalizadores para acelerar las reacciones.